Developments in European standards and regulations for road safety equipment: deciphering the issues and raising questions
Safety barriers are an essential part of our roads and are classified at European level as 'construction products'. This classification means that they must comply with specific rules in accordance with the European regulations governing these products.
This includes CE marking, which guarantees that they meet the required safety and quality standards.
As part of its ecological transition, the European Union has introduced a 'fast track' procedure to speed up the marketing of construction products that meet sustainability criteria.
Regulations (EU) 2024/27 and 2024/69, adopted on 30 May 2024, also impose strict environmental standards to ensure the sustainability of infrastructure.
To help you make sense of the situation, here's a quick decipher...
I. Decoding the jungle of standards
1. A standards context on borrowed time
EN 1317 was introduced in Europe in the 1990s to establish uniform safety standards for road restraint systems such as crash barriers, crash cushions and road markings.
At the time, each European country applied its own regulations, creating safety inconsistencies and obstacles for manufacturers wishing to export their products within the Union.
The official adoption of EN 1317 in 1998 marked a turning point, establishing technical and performance criteria for assessing the ability of devices to protect road users.
In the following years, the standard was revised and extended to cover more scenarios and types of devices, reflecting technological advances and growing road safety needs.
During the 2000s, CE marking became mandatory for all products that comply with EN 1317, signifying their compliance with European requirements and facilitating their free movement within the Single Market.
Since then, the standard has evolved to incorporate new safety and environmental requirements, consolidating a harmonised approach to road safety across Europe.
Although this standard is now familiar to almost all project owners and contractors, it is now on hold due to changes in the European Construction Products Regulation (CPR).
2. What is the CPR?
The Construction Products Regulation (CPR) - EU Regulation No. 305 of 2011 - sets harmonised standards for construction products in the European Union, with the aim of ensuring the free movement of these products while ensuring the safety, health and performance of buildings and infrastructure.
For road restraint systems, the CPR imposes specific criteria in terms of resistance, durability and safety, ensuring their effectiveness in the conditions of use for which they are intended.
These products must be tested and certified in order to comply with European standards, in particular with regard to
1. Mechanical performance: crashworthiness and ability to restrain a vehicle in the event of a collision.
2. Durability: ability to withstand climatic conditions, corrosion and wear to ensure continued performance.
3. Installation: clear instructions for fitting, monitoring and maintaining the equipment.
4. CE marking: a Declaration of Performance (DoP) guarantees that the equipment meets the essential requirements defined in the CPR.
In this way, the CPR has helped to standardise the safety and quality requirements for restraint systems, improving road safety in the EU, and applies to both restraint systems and vertical and horizontal signs.
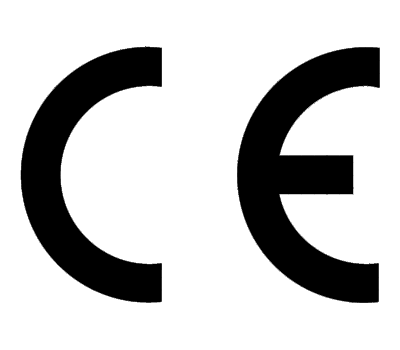
3. Why is Regulation (EU) No 305/2011 being repealed?
A new Construction Products Regulation has been adopted and will enter into force in the second half of 2024, repealing Regulation (EU) No 305/2011.
For a construction product covered by a harmonised technical specification to be placed on the market, the manufacturer must draw up a declaration of performance (DoP) for that product. The manufacturer is responsible for the conformity of the product with the declared performance and the applicable requirements.
When applied to a restraint system, the DoP specifies a number of performance criteria, such as the level of restraint (N2, H1, etc.), the working width (W1 to 8) and the ASI, as well as the Vi and the dynamic deflection (Dn).
This European framework for construction products posed a number of problems, particularly with regard to standardisation and market control.
Feedback received during the evaluation highlighted the need to simplify this framework by reducing duplication and removing inconsistencies that often exist in relation to other European legislation. The aim was to improve legal clarity and reduce red tape for businesses. Unfortunately, this has now made things more complex for economic operators and for our customers who manage and install restraint systems.
The Commission has also identified the construction sector as one of the priority ecosystems facing the greatest challenges in terms of meeting climate and sustainability targets and embracing the digital transformation on which the sector's competitiveness depends.
It has therefore decided to establish rules for the declaration of the environmental performance of construction products, including the possibility of setting relevant thresholds and classes.
The environmental performance classes of products should accurately reflect the diversity of products and their state of the art and allow the most environmentally friendly products to be accurately identified.
Calculations to quantify performance should cover the life cycle of the product, using methods established through standardisation.
For new products, the life cycle calculations should cover all stages of the product life cycle, from the acquisition of raw materials or their production from natural resources to their final disposal.
As we'll see below, steel guardrails offer real advantages in this respect, which are well known and not to be underestimated.
All these new points are included in the new EUROPEAN PARLIAMENT REGULATION. The new CPR contains 94 articles and 11 annexes (the 2011 version contained 68 articles and 5 annexes). The tables in Annex XI of the new CPR provide a quick overview of the correspondence between the articles in the new CPR and those in the 2011 version, as well as showing which articles have been deleted or introduced.
Enjoy your reading...
Link to the new CPR I in English: https://data.consilium.europa.eu/doc/document/PE-12-2024-INIT/en/pdf
4. The Fast Track procedure: an accelerator for sustainable innovation
Manufacturers of road safety equipment are required to adopt a number of eco-responsible practices, including the use of sustainable and recyclable materials, optimisation of production processes and design for recycling.
The fast-track procedure aims to simplify and speed up the certification of sustainable construction products.
It allows European Technical Committees to anticipate and initiate work on the revision of standards for specific products, even if they are not classified as high priority.
In this way, the committees themselves can prepare draft standardisation requests under an accelerated procedure before submitting them to the European Commission.
The aim of this approach is to address persistent delays in the standardisation process and to make it easier for construction products to comply with new legislation.
The aim of this rapid validation process is to meet the growing demand for environmentally friendly products in European infrastructure. Fast Track would offer several benefits to manufacturers:
- Shorter certification times: Products that meet sustainability criteria will be prioritised for assessment, reducing time to market.
- Increased support: Manufacturers committed to sustainable innovation initiatives will benefit from additional advice to ensure compliance with standards, while speeding up the certification process.
The challenge for guardrail manufacturers and their customers is to implement a number of environmentally responsible practices:
- Selecting sustainable and recyclable materials
- Optimising production processes: By integrating energy-saving technologies and favouring renewable energy sources, manufacturers can reduce their environmental footprint and meet the requirements of new regulations.
- Design for recycling: Products must be designed for easy disassembly and recycling to maximise the recovery of end-of-life materials and contribute to the circular economy.
As far as our business is concerned, the technical committee is CEN/TC 226 of the European Committee for Standardisation (CEN), dedicated to road equipment. Its main task is to develop standards and technical specifications for various types of road equipment, in particular
- Safety barriers, including safety cushions, crash barriers, bridge parapets and other restraining devices.
- Horizontal signs: such as road markings and bollards.
- Vertical signs: including traffic signs, cones and delineators.
- Traffic lights: including beaconing, warning and traffic control lights.
- Street lighting: focusing on performance requirements.
- Miscellaneous equipment: including bollards, anti-glare and anti-noise screens.
5. Regulations (EU) 2024/27 and 2024/69: a framework for greener construction
Regulations (EU) 2024/27 and 2024/69 define systems of assessment and verification of constancy of performance (ACVP) to ensure that construction products meet environmental sustainability criteria throughout their life cycle.
These regulations introduce a number of key requirements:
- Factory Production Control (FPC): Manufacturers must implement strict measures to monitor and ensure the environmental performance of products. This includes continuous monitoring of production processes and the use of environmentally friendly materials.
- External audits and environmental testing: Construction products are subject to regular audits and specific tests to assess their compliance with environmental criteria. Audits cover carbon footprint, use of recycled materials and recyclability at end of life.
- Reducing the carbon footprint: Regulations require manufacturers to use low carbon production technologies and encourage the transition to less polluting processes. Products must demonstrate a reduced carbon footprint, measured over their entire life cycle.
- Life cycle and end-of-life considerations: Construction products, such as guardrails, must be designed to facilitate recycling at the end of their life, minimising waste and supporting a circular economy.
The full text of the regulations can be found on the European Commission's EUR-Lex website.
6. Steel: the ideal material to meet new environmental requirements
Among the materials used for restraint systems, steel stands out for its unique ability to be recycled indefinitely, making it a preferred choice for meeting new sustainability requirements.
Steel's recyclability and sustainability benefits include
- Infinite recyclability without loss of quality: Steel can be recycled again and again without losing its mechanical properties. This allows guardrails and other steel barriers to be reused or recycled at the end of their life, reducing the need to mine new resources.
- Reduced carbon footprint: Compared to the production of virgin steel, steel recycling requires much less energy, contributing to a lower carbon footprint. By incorporating recycled steel into their products, manufacturers are meeting regulatory targets for reducing greenhouse gas emissions.
- Increased durability and resistance to climatic conditions: Steel railings are robust, durable and low maintenance. This reduces the frequency of replacement and the environmental impact of repair or replacement work.
- Supporting the circular economy: The use of recycled steel in construction products directly contributes to a circular economy. Guardrails can be easily dismantled, melted down and recycled, limiting the amount of waste.
7. Towards a sustainable infrastructure future?
The new requirements of Regulations (EU) 2024/27 and 2024/69, combined with the "fast track" procedure, represent, according to Europe, a significant step towards the sustainability of European infrastructure and encourage manufacturers to adopt environmentally responsible practices.
Steel, with its infinite recyclability and robustness, is ideally suited to the EU's sustainability objectives.
For vehicle restraint systems manufacturers, steel makes it possible to reconcile safety requirements with a reduced environmental footprint, contributing to more sustainable and resilient infrastructures.
II. Criticisms and points of view
A complex and restrictive European regulatory framework for safety device manufacturers
Steel crash barriers are essential road safety devices, but as manufacturers we face a major challenge: the complexity and overlapping nature of European and national regulations.
Although the objective of safety and durability is laudable, recent legislative developments, in particular Regulations (EU) 2024/27 and 2024/69, increase the administrative and technical burden on manufacturers and will make products more expensive!
Overlapping regulations: a challenge for European manufacturers
The new European environmental standards create an additional layer of specific regulations on top of existing ones, notably the CPR (Construction Products Regulation) and CE marking.
This growing complexity entails significant costs, not only for the certification of each product, but also for ensuring ongoing compliance with increasingly demanding standards, at a time when price remains the main criterion used by local authorities when awarding contracts.
Companies will undoubtedly be forced to increase their expenditure to meet these stringent requirements, which will have an impact on the final cost of the product to road managers and on the overall cost of the infrastructure.
Stringent standards hamper European competitiveness
Compared to other regions of the world, European vehicle restraint system manufacturers face particularly onerous regulations. In North America and several Asian countries, for example, standards are less restrictive, allowing companies to focus more on innovation and production while remaining competitive in the global market.
These differences are directly reflected in prices and time-to-market, which can put European manufacturers at a disadvantage in an already highly competitive industry.
Environmental sustainability: a laudable goal, but difficult to achieve
Going green is certainly a priority, but life-cycle and recyclability requirements, such as the use of sustainable materials and reducing the carbon footprint, apply strictly to each stage of manufacturing.
Although we are all committed to environmentally responsible practices, the multiplication of audits, environmental tests and production controls makes the process more cumbersome.
At a time when the construction sector (public works and civil engineering) is undergoing a profound digital and environmental transformation, these requirements make the practical implementation of a sustainable strategy much more complex and costly.
Sometimes conflicting commitments
What's more, the implementation of these new regulations is not without ambiguity. Duplications and even contradictions between different European directives increase the risk of inadvertent non-compliance, despite companies' best efforts.
This lack of regulatory coherence threatens the competitiveness of European manufacturers, while other regions offer clearer and less restrictive regulatory frameworks.
In my discussions with industry, the example of certain European test laboratories allegedly providing more favourable crash test results is often cited... Shouldn't we solve these problems first, before tackling the regulations, even though there are already many on the subject?
Re-ordering priorities: road safety first!
Before embarking on a revision of the CPR, it would have been appropriate to harmonise the types of vehicles used to test these devices. For example, the lack of tests on bends / curves limits the accuracy of simulations of real conditions and leaves grey areas regarding the effectiveness of crash barriers on winding roads.
In addition, infrastructure development should include higher levels of restraint, particularly for 44-tonne trucks, which are widely used on European roads. These lorries, which pose a high risk in the event of an accident, do not yet have their own restraint systems in the current standard, a shortcoming that is detrimental to infrastructure safety.
In addition, vehicle restraint systems in urban areas require their own specific characteristics, particularly in areas frequented by pedestrians and cyclists. EN 1317, which is mainly designed for main roads, does not take sufficient account of the specific characteristics of urban environments, where modular and adaptable systems would be more appropriate.
Standards need to evolve to adapt to the current realities of roads and vehicles. A revision incorporating these elements would make it possible to offer safer infrastructures adapted to the new environmental and technical requirements of the sector.
Conclusion: Towards the simplification needed to remain competitive
As manufacturers of road safety equipment, we want to meet the European Union's sustainability objectives, which are laudable and essential for our planet and our future existence.
However, in order to remain competitive and not be left behind by competitors from other parts of the world, the regulatory framework needs to be simplified.
Greater harmonisation of standards, reducing duplication and clarifying environmental requirements would be crucial steps towards reducing the burden of compliance while enabling European businesses to innovate and produce sustainably.
To be continued...
Patrick ASIMUS – Managing Director SOLOSAR - 11/2024